Bending sheet metal
Usinage Laurentides offers you its latest generation bending machines and 30 years of experience in bending of metal sheets. We specialize in sheet metal bending services and are fully equipped to meet your needs for bend sheet metal projects. Our sheet metal bending methods expertise in sheet metal fabrication and bending methods sets us apart from other companies in Quebec.
Thanks to our knowledge in various sheet metal bending processes and bending method, we can produce a variety curved shapes of complex parts with any angle and specific shape, offering both series production and turnkey metal transformation. Whether you're looking for a simple bend or complex sheet metal fabrication, we are here to meet your needs.
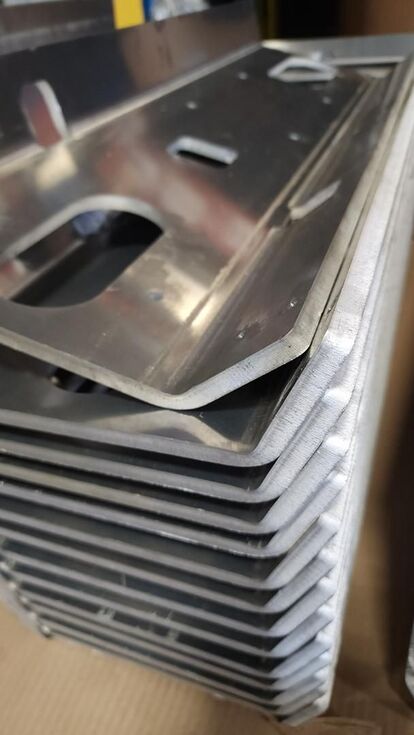
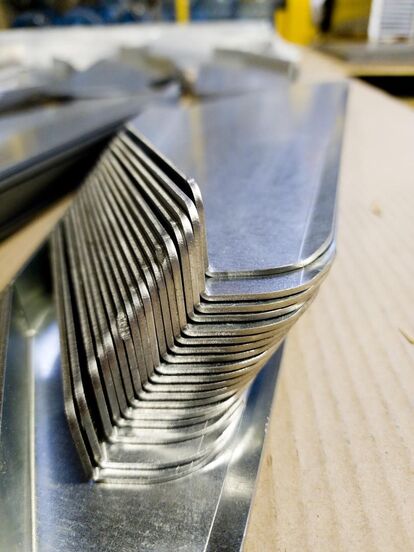
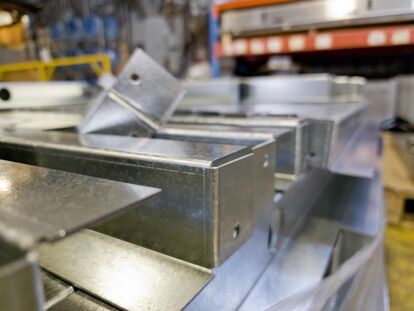
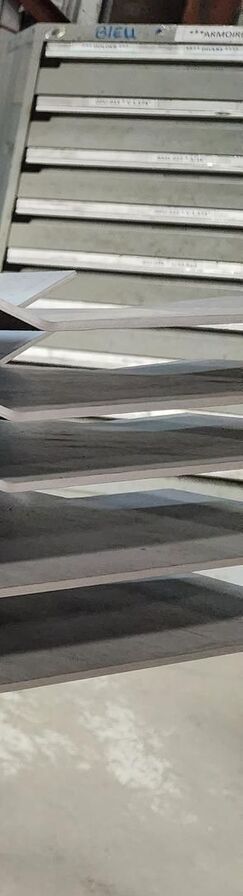
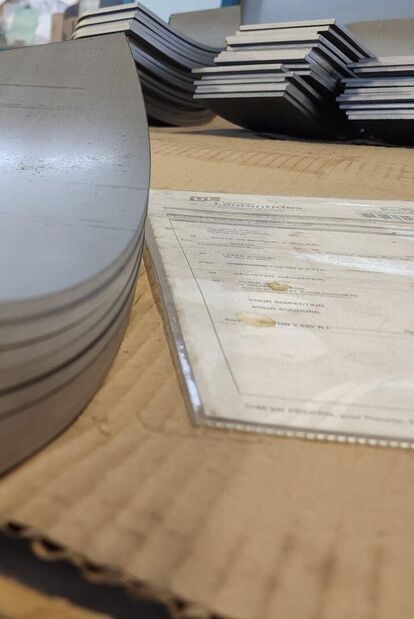
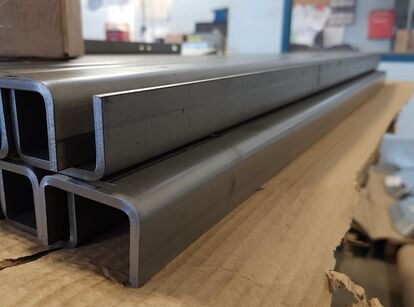
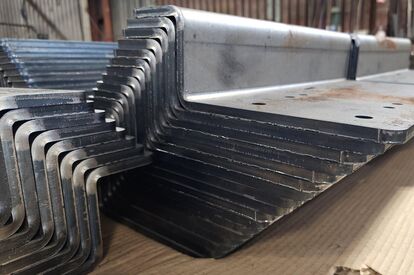
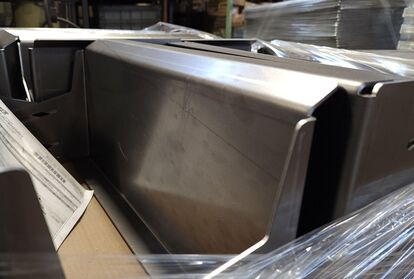
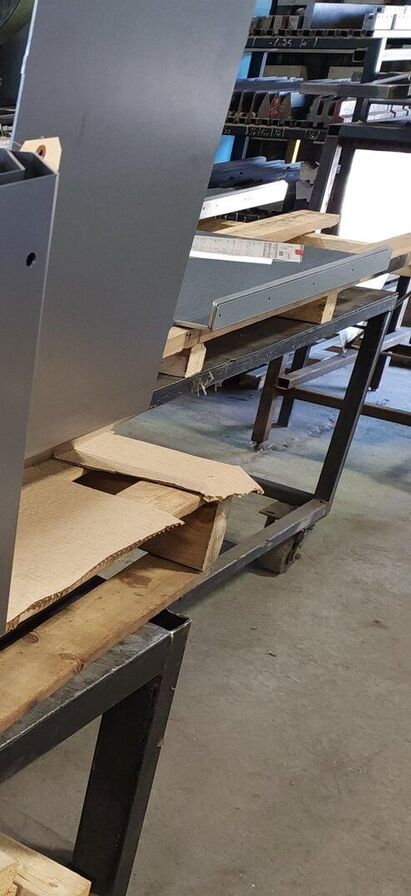
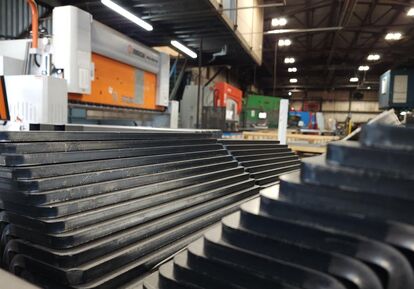
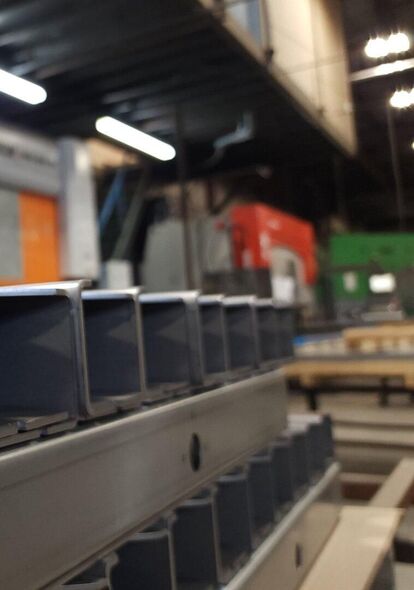
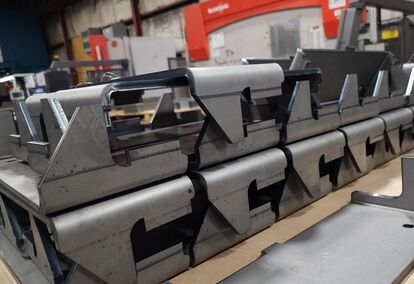
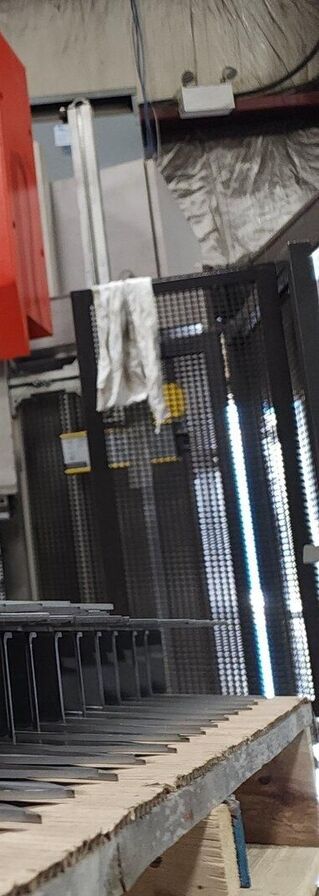
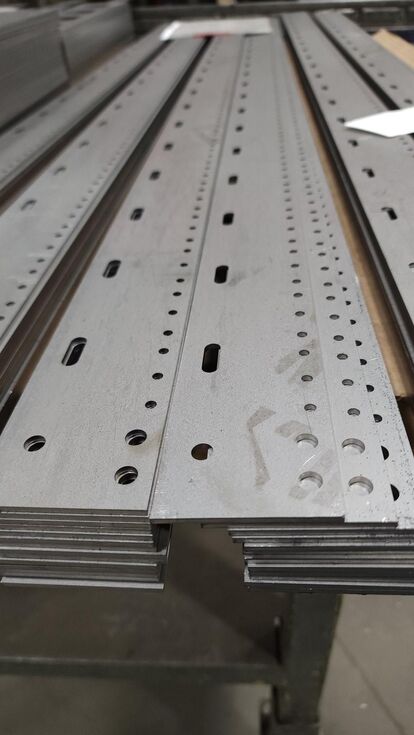
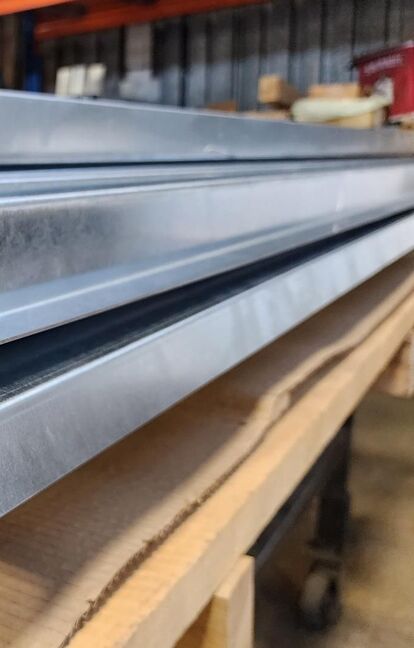
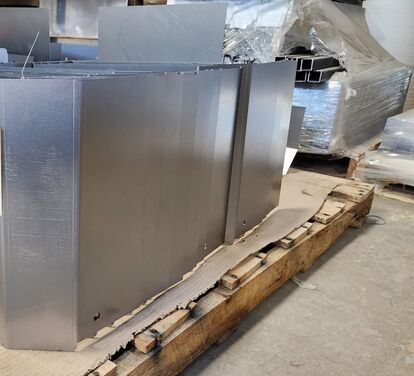
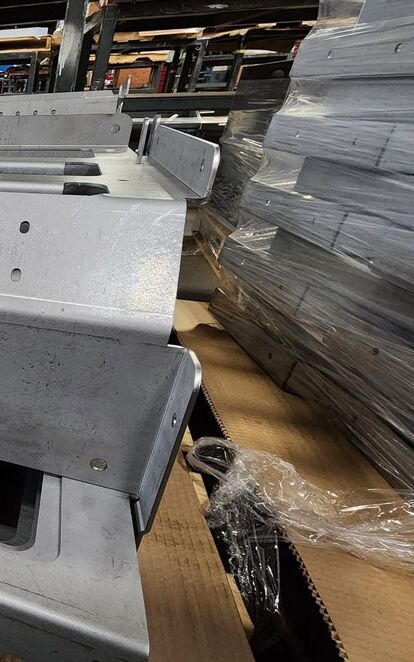
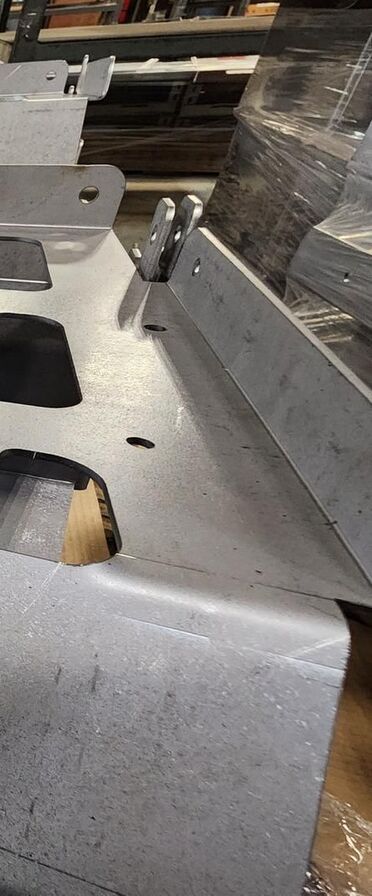
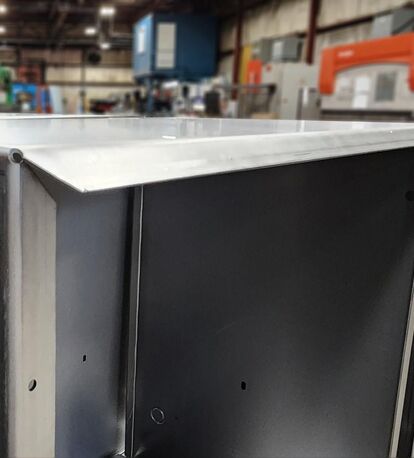
Our bend Sheet Metal Bending Equipment
Our company has a versatile team and several state-of-the-art bending machines, offering a capacity of up to 300 tons and a length of 14 feet. We are specialists in metal processing to offer you a high quality service.
• Coastone Cone C15
• Bystronic Byeler PR 150 IPC
• Emaskan Speed-Bend Pro
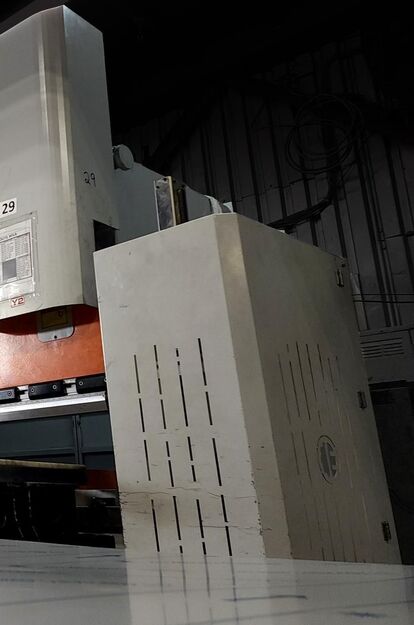
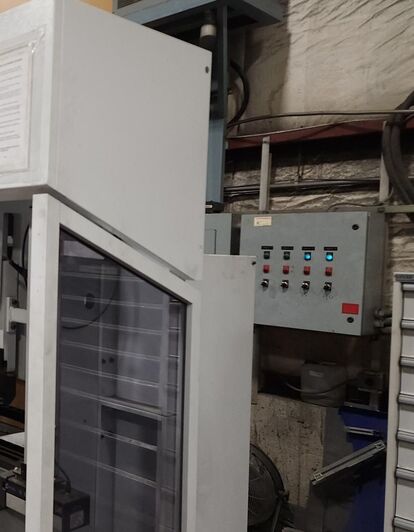
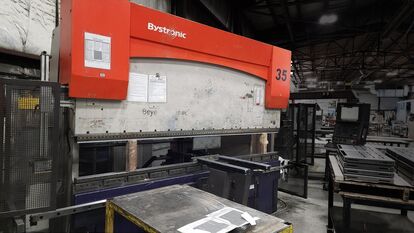
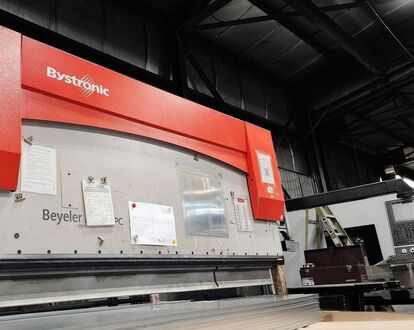
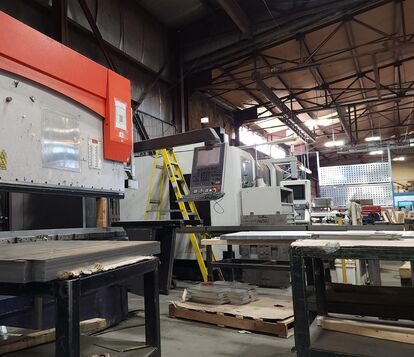
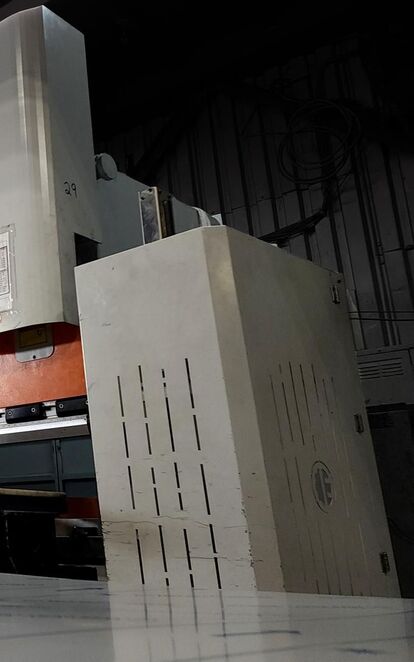
The different varieties of metal plies
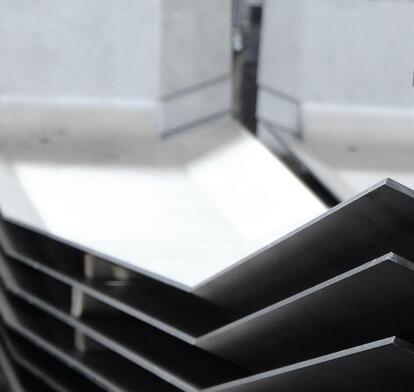
Plis droits des feuilles
Les plis droits offrent une solution pratique pour créer des structures linéaires, des renforts et des pièces structurelles dans de nombreuses applications industrielles.
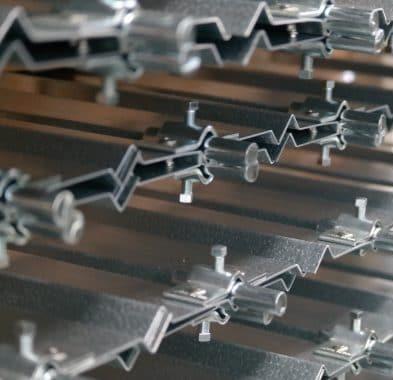
U-folds of sheets
U-bends provide design flexibility and increased strength, making it a widely used bending technique in metal fabrication.
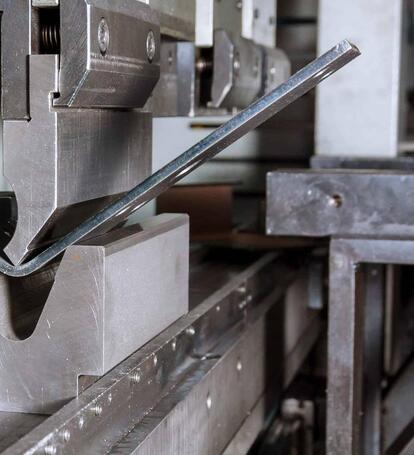
V-folds of leaves
V-bends provide increased strength, attractive aesthetics, and design adaptability, making it a widely used bending technique to meet a variety of manufacturing needs.
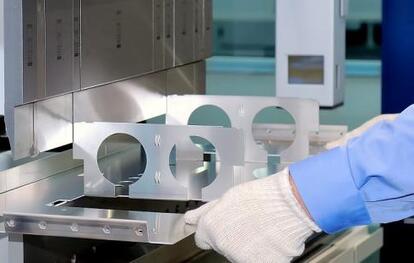
Intricate leaf folds
Intricate bends are made using specialized tools and machinery, as well as expertise in metal design and fabrication. They offer extensive design possibilities, allowing the creation of structures, adapted to the specific needs of each application.
Complex sheet metal bending
Your Excellence Manufacturing Partner in Sheet Metal Bending
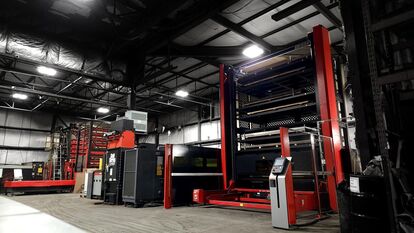
Modern equipment combining speed and precision
Our latest generation equipment combines precision and speed to produce consistent high quality results:
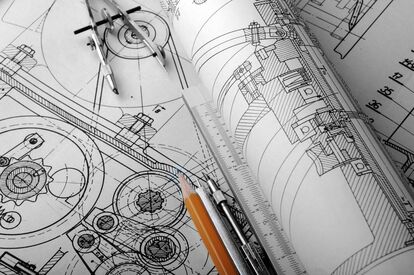
Engineering, Design, and Development of Metal Products
We support manufacturers and specialized design agencies in prototyping, sourcing, and manufacturing innovative products to overcome today's challenges.
- Product R&D
- Industrial Design Agency Partners
- Prototyping and Small Series
- Optimization of Technical Drawings (3D and 2D)
- Modern Equipment Combining Speed and Precision
Manufacturing of Complex Products and Welded Assemblies
Benefit from the efficiency of our bending processes developed in solving the industrial cold bending challenges of our clients for over 30 years.
- Small, Medium, and Large Series
- Finished Metal Products
- Parts Intended for Assembly
- Complex and Unconventional Parts
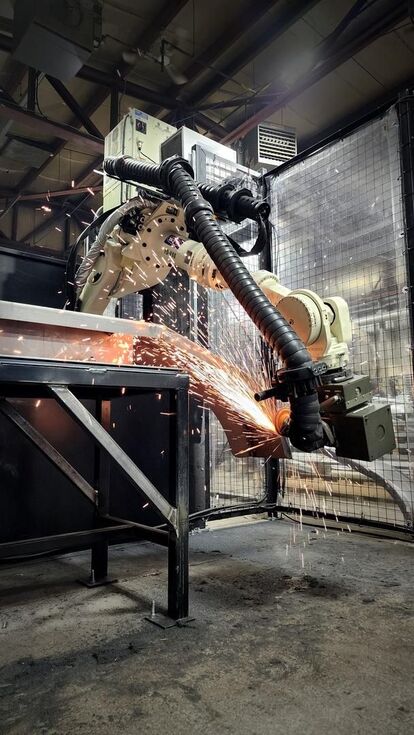
Sheet metal processing
Turnkey solutions for your steel and aluminum sheet processing needs.
- Steel, prepainted, stucco, aluminum & stainless steel
- Complex mechanically welded assemblies
- Numerically controlled cutting (CNC)
- Punching and punch/laser combo
- High precision machining
- Bending metal sheets
- Finishing and surface treatment
- Robotic, spot and manual welding
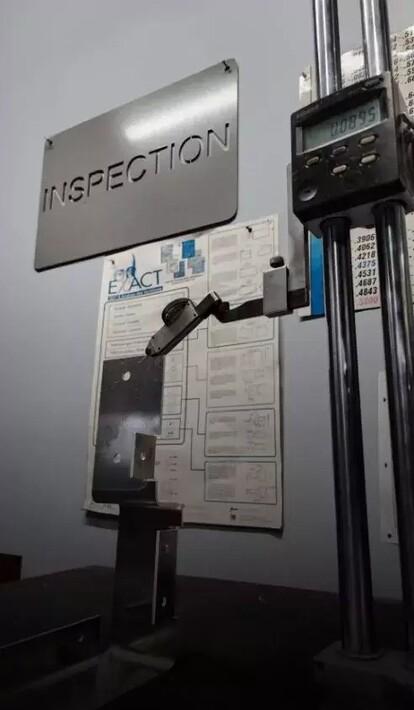
Critical point visual inspection and rigorous quality control
From the revision of technical drawings to the inspection of equipment between our departments, we ensure the delivery of compliant and durable products.
- Validation of Technical Drawings Before Production
- Inspection by Critical Points and Visual
- Updating a Registry of Irregularities
- Production of Non-Conformity Reports (RNC)
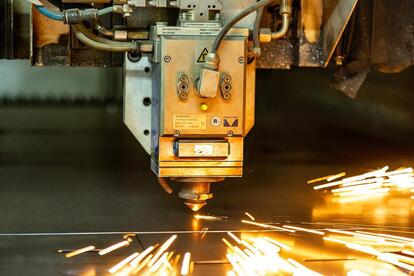
Continuous Supply of State-of-the-Art Metal Production Equipment
Committed to innovation and continuous improvement, our mission is to constantly reinvent our sheet metal bending methods bend materials; to become the unique partner of choice for manufacturers of value-added products in and beyond Quebec.
- Continuous Supply
- Stock Management
- International Import and Export
- Supply Chain Optimization
- Just-In-Time Approach
Frequently Asked Questions About Metal Bending
Why subcontract metal bending to Usinage Laurentides?
- Benefit from our know-how in assembling complex metal parts.
- Modern equipment for precision folding, even in medium or large series.
- Turnkey service, from design to final assembly.
- 360 transformation approach for innovation, plan improvement and cost reduction.
What benders do you use to bend metal?
At Usinage Laurentides, we use seven press brakes to meet your sheet metal bending needs.
- Coastone Cone C15
- Bystronic beyeler pr 150 ipc
- Emaksan Speed-Bend Pro
What is the maximum thickness of sheet metal that can be bent?
Our experts are skilled at handling metal with precision, regardless of its thickness, ensuring a high-quality finish for your parts. We are able to bend metal sheets up to 14 feet wide.
What materials do you fold?
At Usinage Laurentides, we have the expertise to bend a variety of materials including steel. We are able to work with different types of materials, giving you flexibility in your projects.
- Prepainted steel
- Textured stucco steel
- Stainless steel
- Galvanized steel
- Aluminum
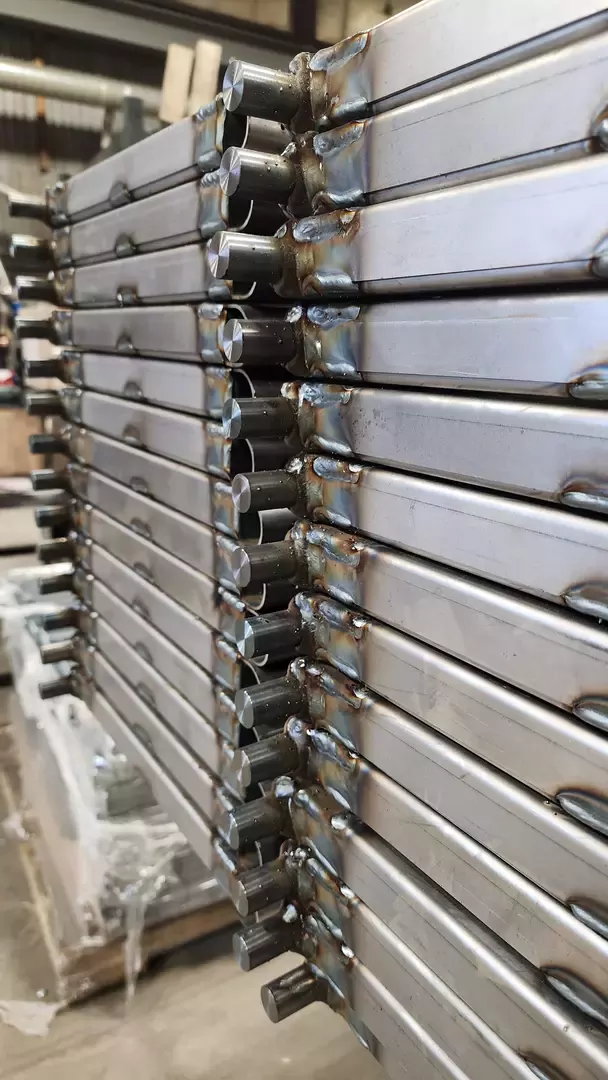
How to find the right supplier for bending sheet metal?
- Get ahead : Don’t wait until you have an urgent need to find a supplier
- Prepare yourself : Have drawings, forecasts, evaluation form on hand
- Communicate transparently : Share your issues and expectations.
- Exchange frequently and keep in touch : The situation of one or other of the parties may have changed, production capacities may no longer be the same, your volumes may have changed.
- Evaluate costs : Compare overall costs to unit costs
- Be precise : Specify potential volumes and supply rate
- Protect yourself : Complete a confidentiality agreement and sign a manufacturing agreement
Quels produits métalliques pouvez-vous plier?
- Complex machined parts for assembly.
- Bending of complex metal parts, including unconventional parts.
- Manufacturing of finished metal products according to specific needs.

What is sheet metal bending?
Sheet metal bending is a processing process in which a sheet of metal is bent to form metal parts with precise angles. This process is used in many industrial sectors for the manufacture of metal products and assemblies.
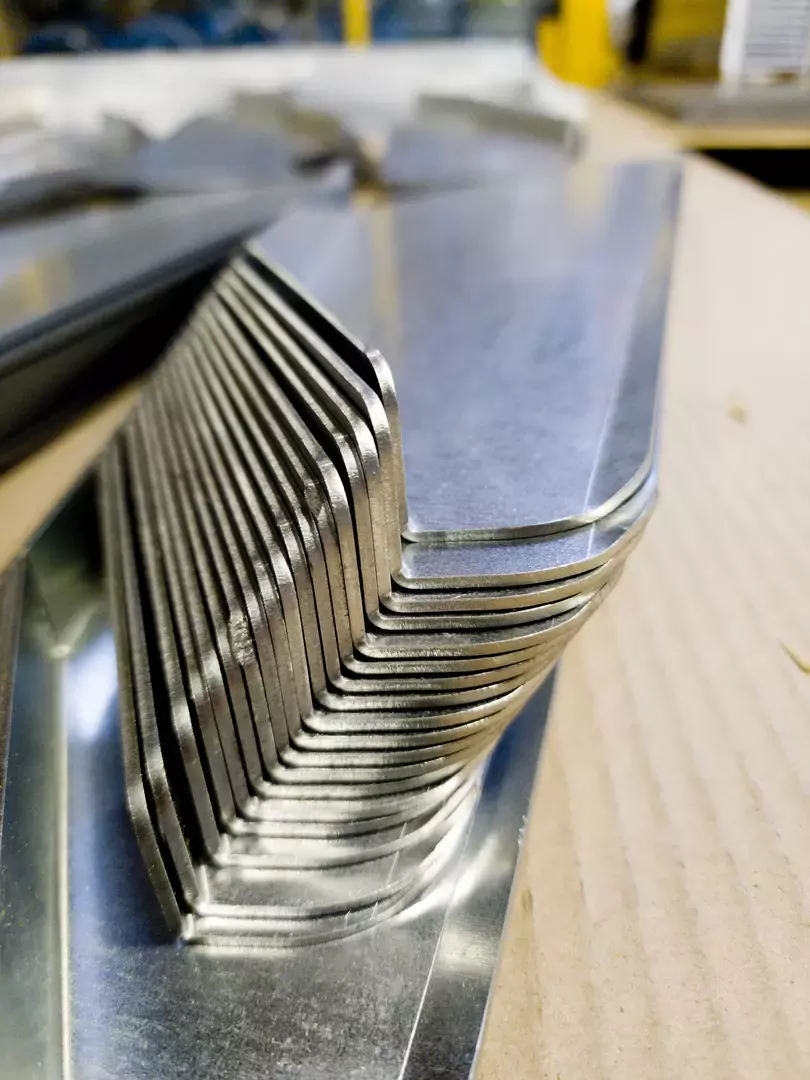
What are the advantages of bending sheet metal?
- Versatility in terms of shapes and dimensions.
- Press brake capacity up to 300 tons and 14 feet long.
What is the production capacity of Usinage Laurentides?
Usinage Laurentides has two factories totaling 40,000 square feet. This allows us to guarantee continuous production, day and night, meeting your needs for tight deadlines and large quantities.
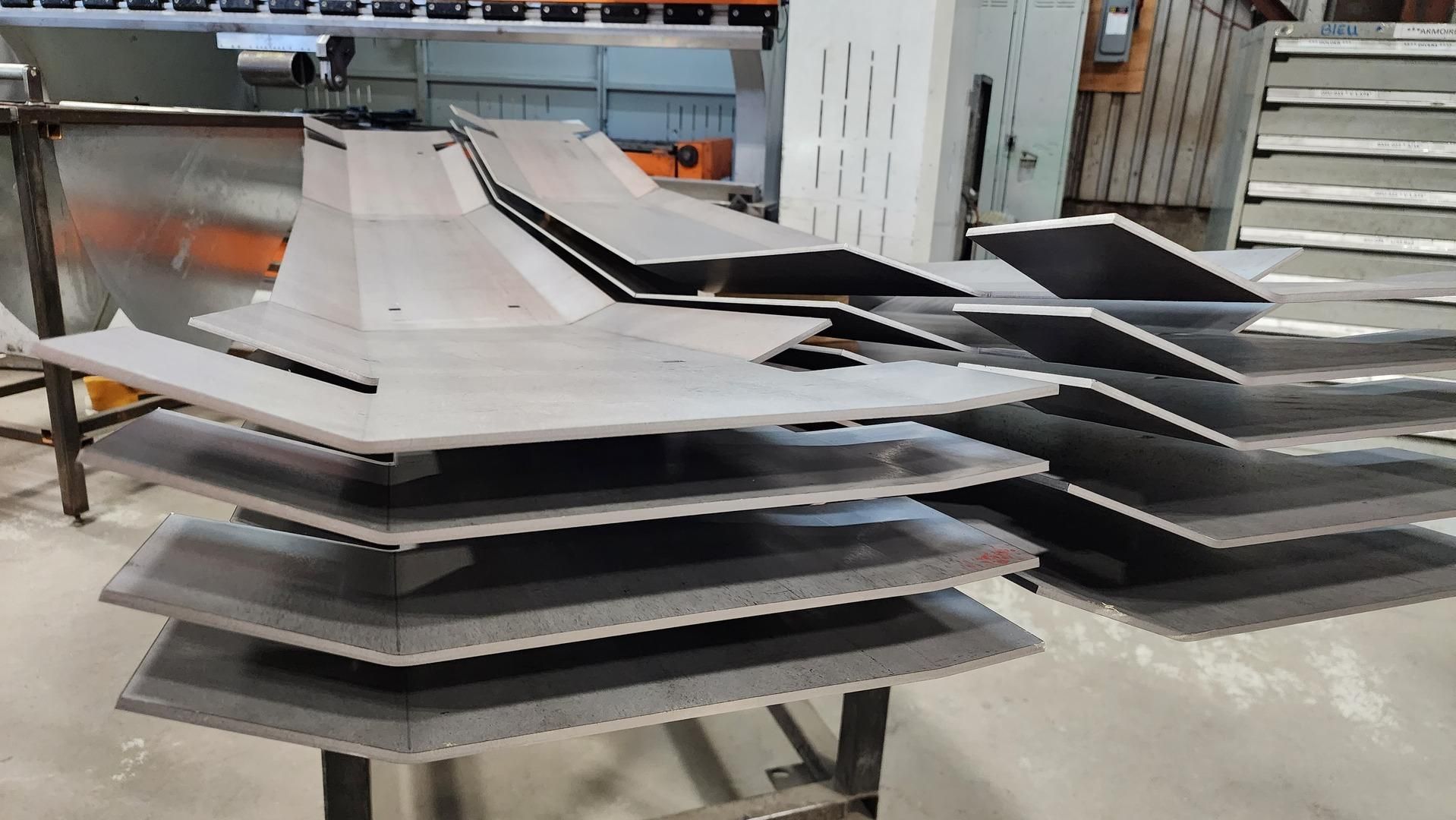
What are the metal bending methods?
There are two main methods of metal bending: air bending and strike bending. Air bending is carried out using our modern equipment, while strike bending is used for parts requiring greater precision.
What is the average defect rate in sheet metal bending?
Our average defect rate in sheet metal bending is less than 1%. We are fast and committed to quality and we use an integrated production system to minimize errors and defects.
Do you have historical data on failure rates during sheet metal bending?
Yes, we have historical data on failure rates during sheet metal bending. Thanks to our integrated production system, our machines are connected to our ERP and we follow a rigorous quality manual. Additionally, each product is inspected according to customer specifications, ensuring consistent quality.
How do you ensure product quality during sheet metal bending?
- Validation of technical drawings before production.
- Visual inspection at critical points.
- Register of irregularities and non-compliance reports (RNC) if necessary.
- Continuous commitment to quality and process improvement.
How do I get a quote for metal bending service?
To obtain a personalized quote, please contact us providing your project specifications, such as dimensions , quantities and specific requirements .
What is the role of bending tools such as punches in the manufacturing process of metal parts?
Bending tools such as punches are essential. They are designed to apply a controlled force to the material and create the desired bend. The different tool shapes and sizes allow for a variety of bends, whether straight bends, U-bends , V-bends or intricate bends .
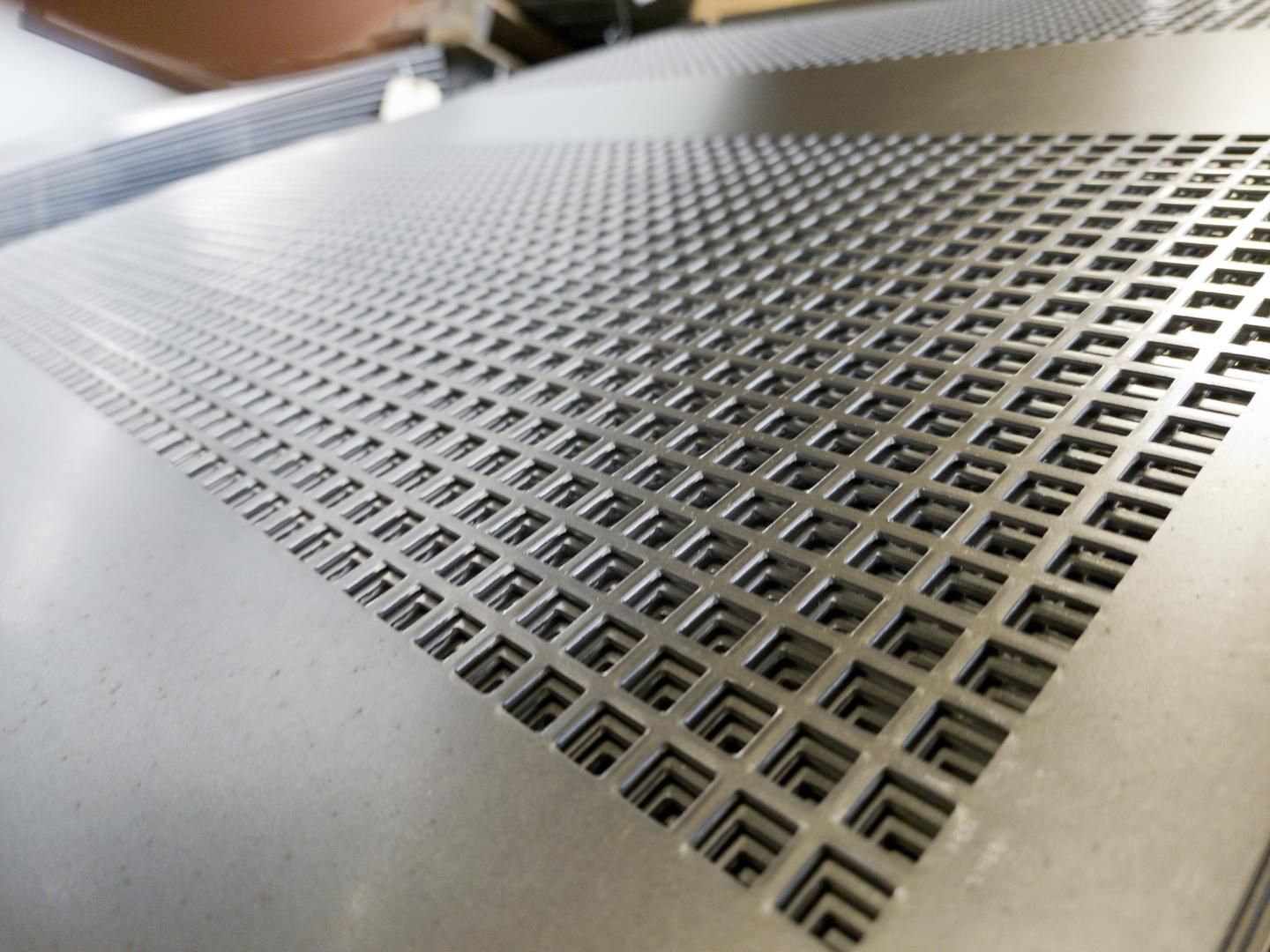
Case Study of bending sheet metal
Metal Bending Service for the Heavy Transport Sector
A leading company in the heavy transport sector, specializing in manufacturing components for industrial vehicles and transport equipment, faced a significant challenge in optimizing and forming the fabrication of essential components shape. The company sought to improve efficiency while ensuring high quality in sheet metal bending shape for the construction of their heavy vehicles. They needed a partner skilled in various sheet metal and materials bending method, especially air bending and roll bending, to bend sheet metals with precision.
The company's main challenges were in the sheet metal bending process, particularly when using the press brake for bending metal sheets. These parts required meticulous forming and bending to ensure both performance and safety. A key focus was on achieving bending method for desired bend angle shape and maintaining the correct bend radius to avoid cracking in bent sheet metal. Additionally, managing material thickness and using the right bending methods to form the sheet metals were crucial.
Usinage Laurentides' Solution
Usinage Laurentides was selected for its expertise in metal and aluminum bending services and its ability to provide a comprehensive manufacturing solution, including sheet metal materials measure fabrication. Our proposal included:
A sheet metal materials bending service integrating cutting-edge technologies to ensure precision in details like bend allowance and k factor.
The capability to work with various metals materials, tailored to the heavy transport sector's needs, including annealed alloy steel and mild steel, with a focus on maintaining the inside bend radius.
Effective management of the production flow to minimize delivery times and maximize material thickness efficiency.
The implementation process bending method involved initial consultations to understand the precise measure needs and technical specifications for the sheet metal materials parts. The use of CNC bending machines ensured unmatched forming results, complemented by rigorous quality testing for each production batch, guaranteeing compliance with high safety standards.
The Results Achieved
Improved Precision and Quality:
The parts produced met the high standards essential for heavy transport vehicles, particularly in terms of bend angles and sheet thickness.
Reduced Production Times:
The efficiency of our sheet metal bending process, including methods like v bending and u bending, reduced production times.
Cost Optimization:
Centralizing sheet metal bending operations helped reduce production and subcontracting costs.
Enhanced Customer Satisfaction:
Our ability to respond quickly and efficiently to requests improved customer satisfaction and loyalty.
In conclusion, Usinage Laurentides' expertise in the sheet metal bending process and comprehensive manufacturing capabilities allowed the client company to streamline forming edge production, improve the quality of its products, and reduce costs. Our strategic partnership optimized manufacturing processes and achieved efficient operational objectives, demonstrating the importance of skilled sheet metal bending in industrial applications.